We’re beginning off with plenty of supplies information in at this time’s 3D Printing Information Briefs, from Replique, Asahi Kasei, and Arkema; plus, a crew of researchers are 3D printing metals with contrasting properties. Talking of analysis, Georgia Tech researchers are utilizing UV mild, as a substitute of excessive temperatures, to 3D print glass microstructures, whereas researchers from the College of Oxford are 3D printing neural cells that mimic mind structure. Lastly, a College of Mississippi analysis crew developed a 3D printed movie that helps cervical most cancers analysis, and BellaSeno has a novel manufacturing workflow for custom-made, 3D printed bone scaffolds.
Replique Launches Open Materials Database for AM at Formnext
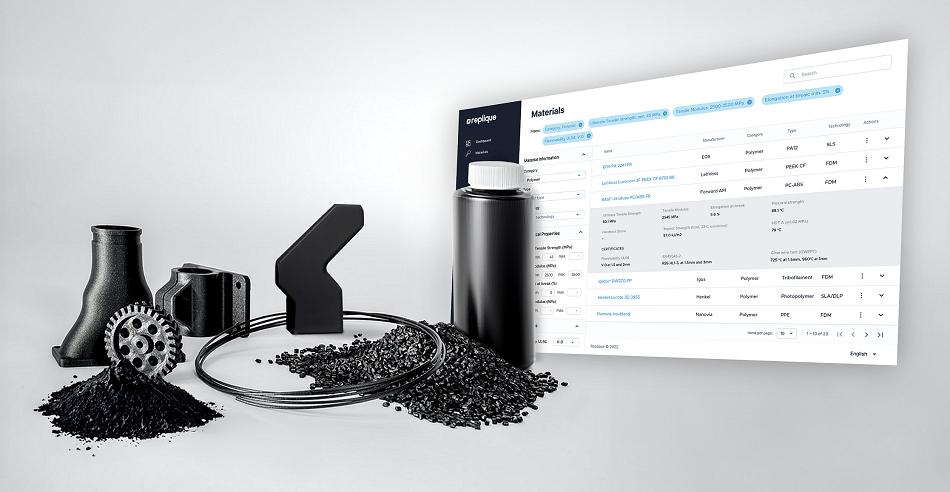
On the latest Formnext 2023, Replique, which gives a decentralized 3D printing platform for safe dependable manufacturing of industrial-grade elements, introduced the launch of a complete, open materials database for 3D printing. For AM tasks to achieve success, you want the correct supplies, however the analysis course of for locating the correct one is labor-intensive. Replique’s new database streamlines and simplifies materials choice, providing customers an intuitive platform—with help from its trusted materials companions—that saves money and time. There are a selection of filtering choices, reminiscent of trade requirements, utility fields, and technical specs, and sooner or later, the platform may even present fast entry to reference instances and certificates. It’s an open system, so printer producers, service suppliers, and end-users will all profit, and can even contribute to the database with their very own materials insights.
“Via our every day engagement with materials information, we now have constructed a wealthy data hub that we are actually desperate to share with the broader group,” defined Dr. Henrike Wonneberger, CEO and Co-Founding father of Replique. “The launch of our materials database represents one other vital step in our mission to drive the industrialization of additive manufacturing and supply complete help to our prospects at each stage of their journey.”
Asahi Kasei Begins Gross sales for 3D Printing Filaments in North America
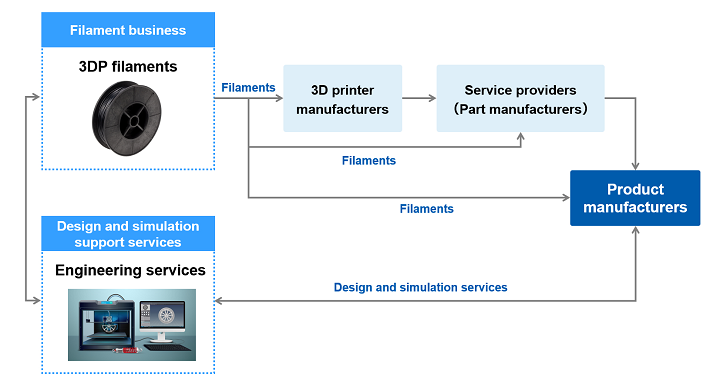
The Asahi Kasei Group, based in 1922 and now boasting 48,000 workers worldwide, is increasing to the North American 3D printing market with filament gross sales by way of Asahi Kasei Plastics North America, Inc. (APNA), which manufactures high-performance, engineered polymers and chemically coupled polypropylene resins. APNA will advance two AM-focused enterprise initiatives, beginning with profitable filament gross sales in North America after which a worldwide enlargement. The mushy launch will begin with filaments from the XYRON modified polyphenylene ether (mPPE) resin product line, with properties together with warmth resistance, influence power, and printability, after which develop to incorporate the Thermylene polypropylene (PP) group, which options creep and chemical resistance, excessive tensile power, and elevated temperature efficiency.
APNA additionally has established computer-aided engineering (CAE) companies, which have been expanded to 3D printing to supply help for filaments. In Could, Asahi Kasei Company Enterprise Capital (CVC) invested in CASTOR Applied sciences to broaden its CAE, and the 2 are actually growing a singular 3D printing software program, which incorporates automation of superior simulations. So its second AM-focused enterprise initiative will give attention to buyer help with superior assets by way of CAE.
Arkema Partnering with AM Leaders to Develop Subsequent-Gen Supplies
To proceed providing its prospects extra high-performance, sustainable 3D printing supplies, like its bio-sourced Rilsan® Polyamide 11, Arkema has introduced new partnerships with a number of trade leaders. At Formnext 2023, the group showcased its vary of superior 3D printing supplies, together with materials options from its new companions. Collectively, Arkema and HP launched a brand new polyamide 12 powder for Multi Jet Fusion, referred to as 3D Excessive Reusability PA 12S, for manufacturing of practical elements, and the corporate additionally collaborated with GENERA on 3D printed personalised eyewear, utilizing GENERA’s automated DLP course of and Arkema’s N3xtDimension UV-curable materials N3D-GEN976.
Arkema and Fast Form are working to push AM ahead by way of a spread of customized UV-curable N3xtDimension formulations tailor-made for prime efficiency within the latter’s DLP printers, and the corporate can be persevering with its journey with software program supplier 3YOURMIND to broaden the Easy3D digital platform for superior materials suggestions and on-demand improvement; the hot button is adopting N3xtDimension liquid resins. EOS firm Superior Laser Supplies is collaborating with Arkema to supply PEKK-100 powder—based mostly on Kepstan PEKK—to EOS P810 customers to be used in demanding industries, like aeronautics. Lastly, French service bureau Erpro 3D Manufacturing unit developed an built-in provide chain in Europe for SLS 3D printed customized elements made with Arkema’s Pebax Rnew elastomers.
Researchers 3D Printing Personalized Steel Components with Completely different Properties
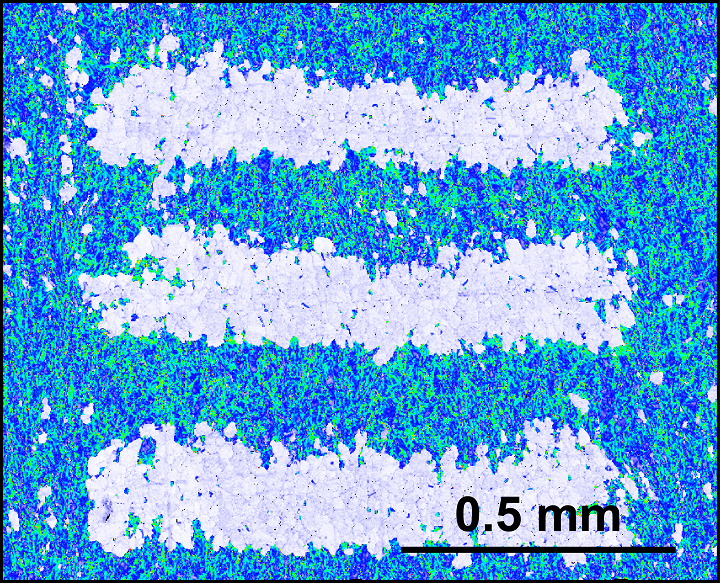
A crew of researchers, led by the College of Cambridge and Nanyang Technological College, Singapore (NTU Singapore), got here up with a new methodology to make custom-made 3D printed steel elements with completely different properties, like having some areas of steel elements stronger than others. Impressed by conventional “heating and beating” strategies utilized in blacksmithing, the interdisciplinary crew mixed supplies science, mechanical engineering rules, and 3D printing methods usually used to take away and forestall defects in metals, and developed a way that may alter microscopic buildings within the metals to alter their properties. Moreover, the tactic makes it potential to resolve what sort of inner microstructure, and sort of property, you need, and the place it may be fashioned within the steel. Theoretically, producers may use this course of to design steel elements with options like completely different ranges of corrosion resistance or electrical conductivity. You may study extra within the crew’s analysis paper.
“Our methodology opens the best way for designing high-performance steel elements with microstructures that may be finetuned to regulate the elements’ mechanical and practical properties, even at particular factors, and permitting them to be formed in advanced methods with 3D printing,” defined Professor Gao, from NTU’s College of Mechanical and Aerospace Engineering (MAE).
Different scientists on the crew have been from the Company for Science, Know-how and Analysis (A*STAR)’s Singapore Institute of Manufacturing Know-how (SIMTech); A*STAR’s Institute of Excessive Efficiency Computing (IHPC); Switzerland’s Paul Scherrer Institut (PSI); the VTT Technical Analysis Centre of Finland; and the Australian Nuclear Science and Know-how Organisation (ANSTO).
Georgia Tech 3D Printing Glass Microstructures with UV Gentle and Low Temperatures
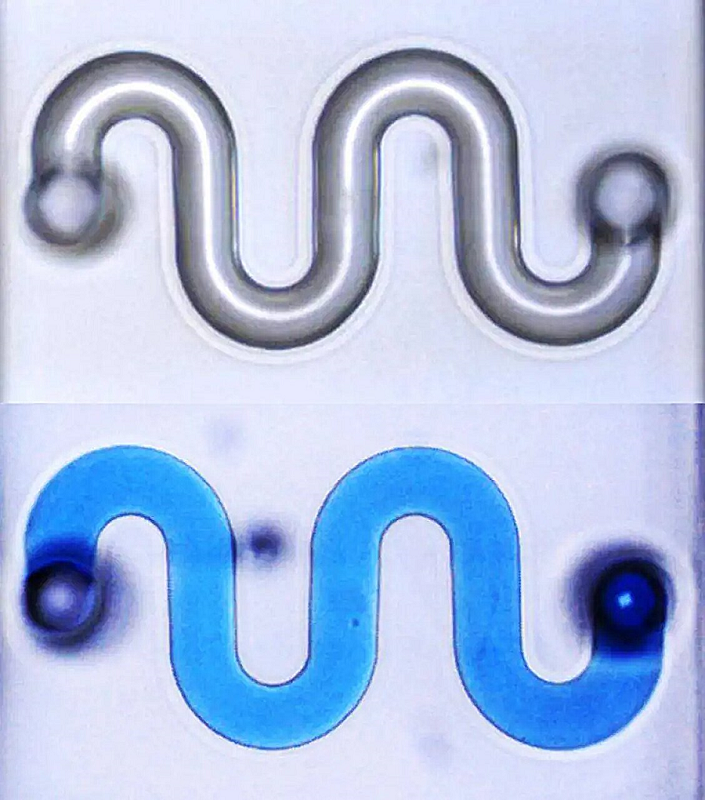
As an alternative of counting on very excessive temperatures, researchers on the Georgia Institute of Know-how (Georgia Tech) have developed a brand new course of for 3D printing glass microstructures that makes use of quick ultraviolet (UV) curing. The tactic shortens curing time from 12 hours to 5, and reduces the warmth wanted to transform printed polymer resin to silica glass from 1,100°C to round 220°C. Sometimes, 3D printing glass requires burning away polymer mixtures as soon as the ultimate form is fashioned, however the crew used a light-sensitive photoresin, based mostly on mushy PDMS, that’s transformed to glass utilizing deep UV mild, which permits the decrease temperatures that save heating vitality. Plus, they don’t have so as to add silica nanoparticles, which implies fewer assets are concerned. As they clarify of their analysis paper, the crew’s course of might be used print tiny glasses lenses for medical gadgets and imaging, in addition to microfluidic gadgets and microelectronics with glass buildings.
“This is without doubt one of the exploratory examples displaying that it’s potential to manufacture ceramics at gentle situations, as a result of silica is a sort of ceramic. It’s a very difficult drawback,” defined George W. Woodruff College of Mechanical Engineering Professor H. Jerry Qi, who led the analysis. “We’ve a crew that features individuals from chemistry and supplies science engaged in a data-driven strategy to push the boundary and see if we are able to produce extra ceramics with this strategy.”
College of Oxford 3D Printing Neural Cells to Restore Mind Accidents
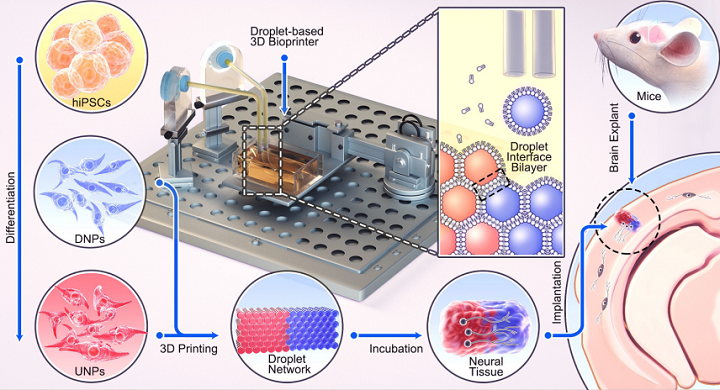
Mind accidents, attributable to stroke, tumor surgical procedure, and trauma, most frequently lead to main injury to the outer layer of the mind, referred to as the cerebral cortex, which causes difficulties with communication, cognition, and motion. Tissue regenerative therapies may someday assist deal with mind accidents, however till now, there hasn’t been a method to make sure that implanted stem cells mimic human mind structure. However a examine out of the Oxford Martin Programme on 3D Printing for Mind Restore may assist change that: for the primary time, researchers confirmed that neural cells will be 3D printed to imitate the structure of the cerebral cortex, which is promising for repairing mind accidents.
The crew made the cortical construction with human induced pluripotent stem cells (hiPSCs), which have been differentiated into neural progenitor cells for 2 completely different layers of the cerebral cortex and suspended in answer to create two bioinks; these have been used to print a two-layered mind tissue construction. When the printed tissue was implanted into mouse mind slices, the cells confirmed sturdy integration, in addition to signaling exercise, which signifies that the mouse and human cells have been speaking. The researchers plan to refine their droplet printing approach additional to make advanced, multi-layered cerebral cortex tissues that may mimic the structure of the human mind much more realistically.
Cervical Most cancers Drug Supply Choices May Enhance with 3D Printed Movie
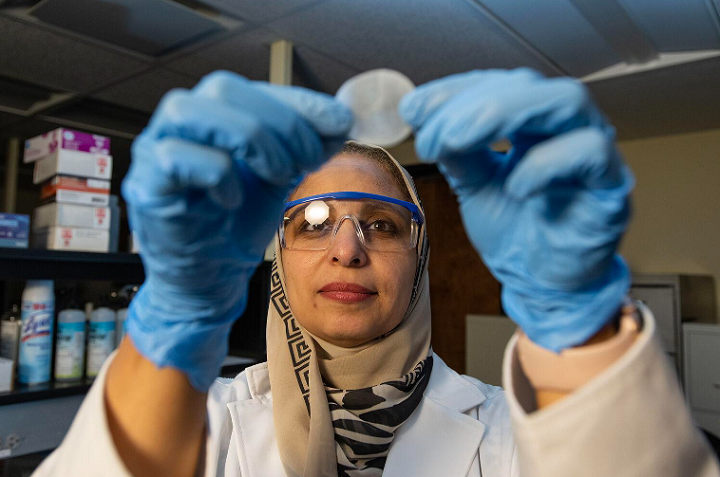
(Photograph courtesy of Thomas Graning, UM)
In response to the Facilities for Illness Management and Prevention, about 4,000 girls die of cervical most cancers annually within the U.S., and Mississippi has the second highest age-adjusted cervical most cancers mortality within the nation, with 3.4 deaths per 100,000 girls and women a yr. Researchers on the College of Mississippi (UM) are working to enhance drug supply of disulfiram, which reveals promise as a most cancers remedy. Most drugs are oral, which might have absorption points and unwanted effects, however vaginal supply is extra focused, and that’s what the crew centered on of their analysis. They used hot-melt extrusion (HME), which includes melting a cloth and reshaping it whereas it cools, to supply drug-loaded filaments, after which 3D printed the exact dosage. Disulfiram is heat-sensitive, which might be problematic for vaginal supply, so the crew optimized the drug’s design, and the processing temperatures of HME, to create a movie—enabling drug supply on to the goal website.
“Vaginal drug supply affords focused, localized supply. The vaginal movie’s sticking properties assist prolong the movie’s retention and the drug launch, which is an added benefit,” mentioned Eman Ashour, Assistant Professor of Pharmaceutics and Drug Supply.
“The outcomes of this user-inspired examine will contribute to enhancing affected person outcomes and remedy alternate options. “We hope to construct new applied sciences based mostly on this undertaking’s success and discover different illness states and makes use of sooner or later.”
BellaSeno’s Manufacturing Workflow for 3D Printed Bone Scaffolds Introduced
Lastly, BellaSeno GmbH, a German medtech firm, introduced information in regards to the novel workflow for its custom-made, 3D printed bone scaffolds on the German Congress of Orthopaedics and Traumatology (DKOU 2023). It’s one of many first corporations to current an MDR-compliant (Medical Gadget Regulation) and ISO 13485 audited workflow for the design and manufacturing of customized, 3D printed, resorbable polycaprolactone (PCL) scaffolds for treating massive (> 5cm dimension) segmental bone defects together with an autologous bone graft. With a majority of these accidents, scaffolds maintain the bone graft in place for optimum therapeutic and vascularization, and 3D printing permits the manufacturing of patient-specific ones. In BellaSeno’s workflow, 3D reconstruction is used to digitally section the CT scan, and the corporate then follows the treating surgeon’s course to create an anatomically-oriented design to fill the defect. After parameters are adjusted to customise the scaffold’s match and mechanical efficiency, FDM know-how is used to print a prototype, which is shipped to a practitioner for “design freeze” and biomechanical testing. The ultimate scaffold is manufactured underneath cleanroom situations, and completed with post-processing and sterilization.
“This particular workflow permits a really time- and cost-effective manufacturing course of for patient-specific scaffolds whereas complying with highest regulatory requirements. Relying on the specified properties of the scaffolds, the merchandise can soak up static non-deformable axial forces of as much as 4,000 N or shorten by as much as 1cm underneath a load of as much as 1,000N in a managed method with out breaking,” defined Dr. med. Tobias Grossner, Chief Medical Officer of BellaSeno. “This leads to a brand new technology of high-performance bone scaffolds that are nicely fitted to the organic reconstruction of enormous bone defects.”
Subscribe to Our E-mail Publication
Keep up-to-date on all the most recent information from the 3D printing trade and obtain data and affords from third occasion distributors.